Zenith – Industry Leading Specialists in the Inspection, Structural Analysis & Refurbishment of Steel Chimneys
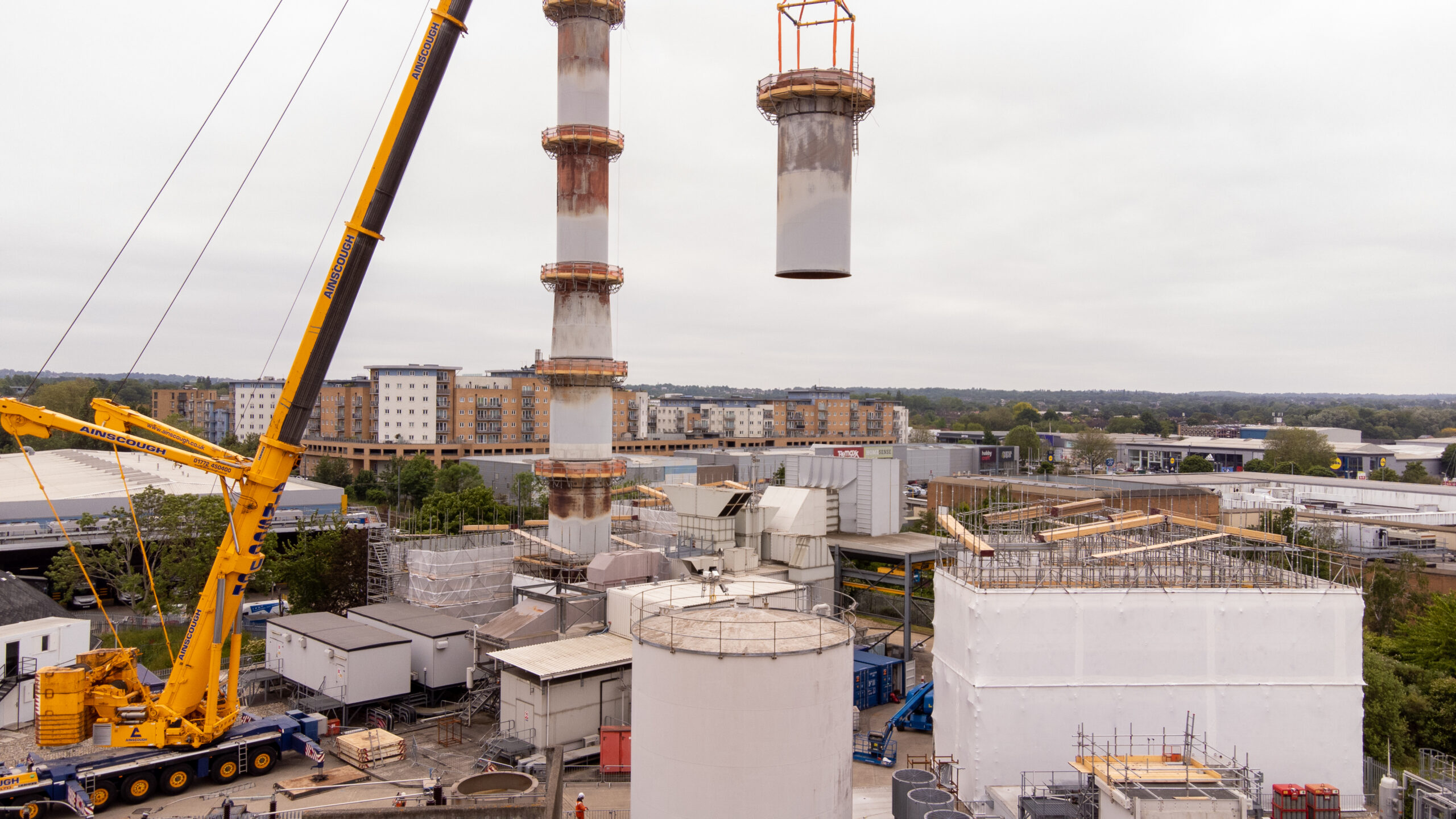
Zenith has a global reputation for innovation and excellence. We provide world class engineering services, inspections and structural analysis, industry leading specialist access capabilities, heavy lifting at height and comprehensive mechanical services.
Croydon Power Station is a gas power plant in Greater London that generates 50 MW of power. It has a 67m free-standing double-skinned steel chimney that discharges waste gas from the gas turbine. The chimney is fabricated in eight sections comprising an external mild steel windshield with an internal 304 grade stainless steel flue liner, also in eight sections. Following an initial inspection, it was observed that the steel windshield paint had deteriorated at a number of levels and the probable reason for the localised high temperatures was that the insulation between the liner and windshield had slipped down the liner, exposing the upper outside of each liner plate section.
In addition to the inspection, Zenith’s engineering team carried out a design assessment following which recommendations were made to disassemble, refurbish and re-erect the chimney. Zenith engineering team designed an innovative access solution, which Zenith’s on-site team installed and used to safely undertake the refurbishment works. Once the chimney had been dismantled and following further inspection, extensive strengthening works were undertaken:
• New insulation retaining pins were installed on the internal liner as part of the refurbishment project. The spacing was determined in accordance with current standards.
• Many of the liners’ in-situ gussets were reprofiled and rewelded or removed and replaced, and together with necessary welding to the liner, the flanges and the liner were strengthened.
• Over plating was also carried out to the silencer.
• Extensive welding repairs were undertaken on the steel windshield.
During the dismantling phase, each section was placed within a temporary adjacent structure to provide section support, suitable access as well as the encapsulation of each section which enabled the following refurbishment works to be completed:
• Surface preparation of carbon steel surfaces using abrasive blasting media.
• Remedial strengthening work to chimney sections.
• Installation of replacement insulation to the chimney flue liner sections.
• Application of high temperature/protective paint system to the internal and external windshield.
After successful completion of the refurbishment works, the chimney was systematically re-erected into position.
Utilising all of Zenith’s world class innovative engineering capabilities together with our on-site excellence in safe project execution, we remain at the forefront of the industry providing our blue-chip clients in the power, oil, gas, petrochemical and cement industries with an unrivalled level of performance.
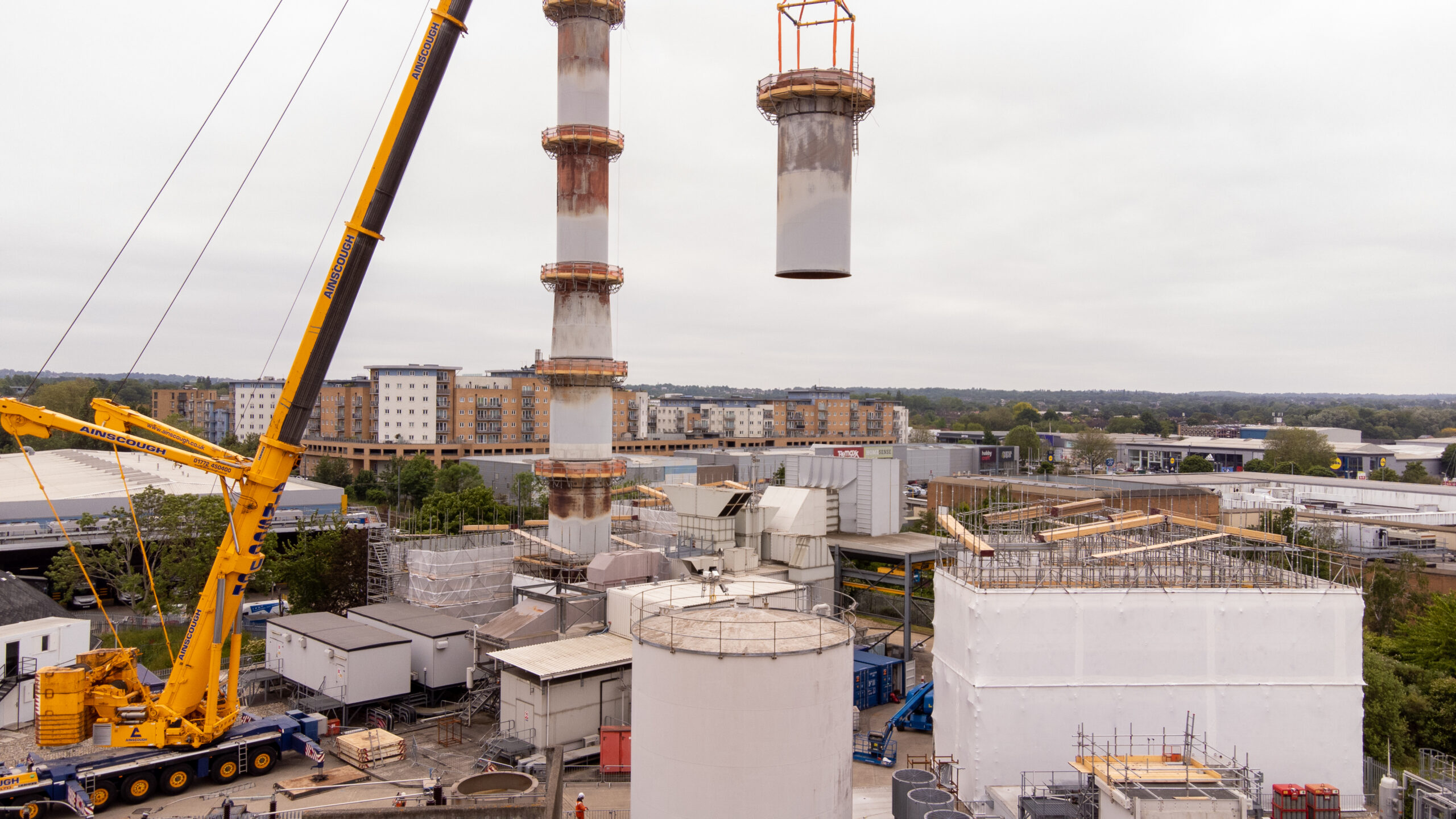