New Steel Chimney Erection
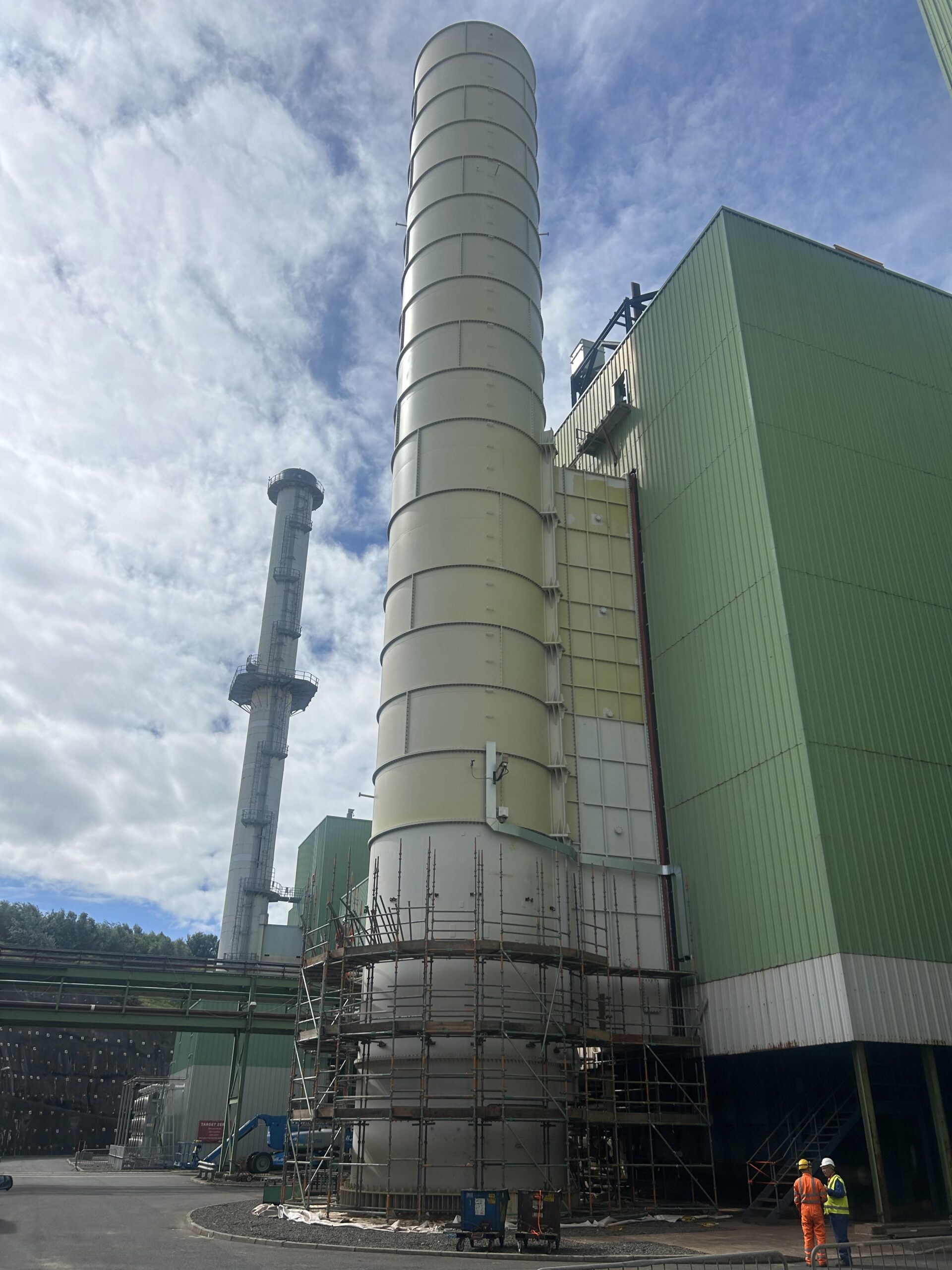
Zenith constantly brings first class structural analysis and inspection services together with innovative access and repair solutions for the world’s leading blue-chip companies in the power industry.
Notably, when it comes to the inspection, structural analysis, specialist access, repair and maintenance of industrial chimneys, Zenith is the leading industry specialist in the country with a world-class in-house engineering team combined with highly qualified site operatives providing excellence in all of our activities.
Following the recent failure of a gas-fired power station steel chimney at EP UK’s Ballylumford Power Station, Zenith safely and successfully dismantled the failed chimney down to the 25m level which consists of 10.255m for the remaining steel chimney and 14.885m for the remaining associated inlet duct. The decision was made to potentially retain the lower section of the existing chimney and inlet duct and to design, fabricate and erect a replacement steel chimney in position atop of the retained base. Once a comprehensive access scaffold was designed and installed internally and externally and following the removal of the external insulation and cladding, the full external surface of the retained chimney base and inlet duct was grit-blasted and non-destructive tests (ultrasonic thickness checks) were performed to establish any section loss. In addition, a visual inspection was undertaken to identify any defects and establish the condition of the retained section.
As a result of the survey, the decision was made to retain the lower base section and inlet duct. Although the original height of the chimney was 75m, the replacement temporary steel chimney would stand at a height of 50.8m.
Defective, damaged and distorted sections of the retained chimney and ductwork were cut out and replaced as well as additional stiffening being added at the duct entry point consisting of HEM450 vertical reinforcing (goal post columns), horizontal reinforcement, horizontal stiffening and flanges.
A new base flange was designed and installed at the 10.255m level to accept the new chimney sections with an outer diameter of 6216mm. The replacement chimney shell was constructed in externally flanged sections using 8mm, 10mm and 12mm thick plate from S355J2 carbon steel. Accessories such as the profiled horizontal flanges were fabricated from S355J2 carbon steel. The chimney shell was fabricated parallel throughout its height and each section was split into two rings. Each ring was split vertically into 3 x 120 degree segments complete with 100mm x 20mm profiled vertical locating flanges. All flanges were secured with grade 8.8 galvanised bolts.
The chimney sections and replacement ducting were individually constructed adjacent to the chimney location and were lifted into position. A new expansion joint was installed. Cable tray supports and eight gas sampling ports were welded to the chimney shell at the 12m and 40m levels.
Zenith’s world class engineers, first class inspection engineers and industry-leading on-site access and mechanical specialists reacted immediately when called upon to ‘make safe’ the failed steel chimney at Ballylumford. Including the replacement chimney, Zenith provided a comprehensive solution to allow the gas-fired power station to re-commence its energy production.
Zenith provides an unrivalled level of service, and we bring innovation and excellence to all our activities. We are often called upon by the world’s leading companies in the oil, gas and power industries to provide unique solutions that prove to be safe, time efficient and industry firsts.
Please click on the link below to watch our timelapse video including additional specialist services we provide to our blue chip clients:
EP UK Ballylumford New Steel Chimney |
Technical Alert – Steel Chimneys |
Zenith’s World Class Engineering Services |
Mechanical & Welding Services |
Major Steel Chimney Refurbishment – VPI |
Steel Chimney Refurbishment – Whitetower Croydon |
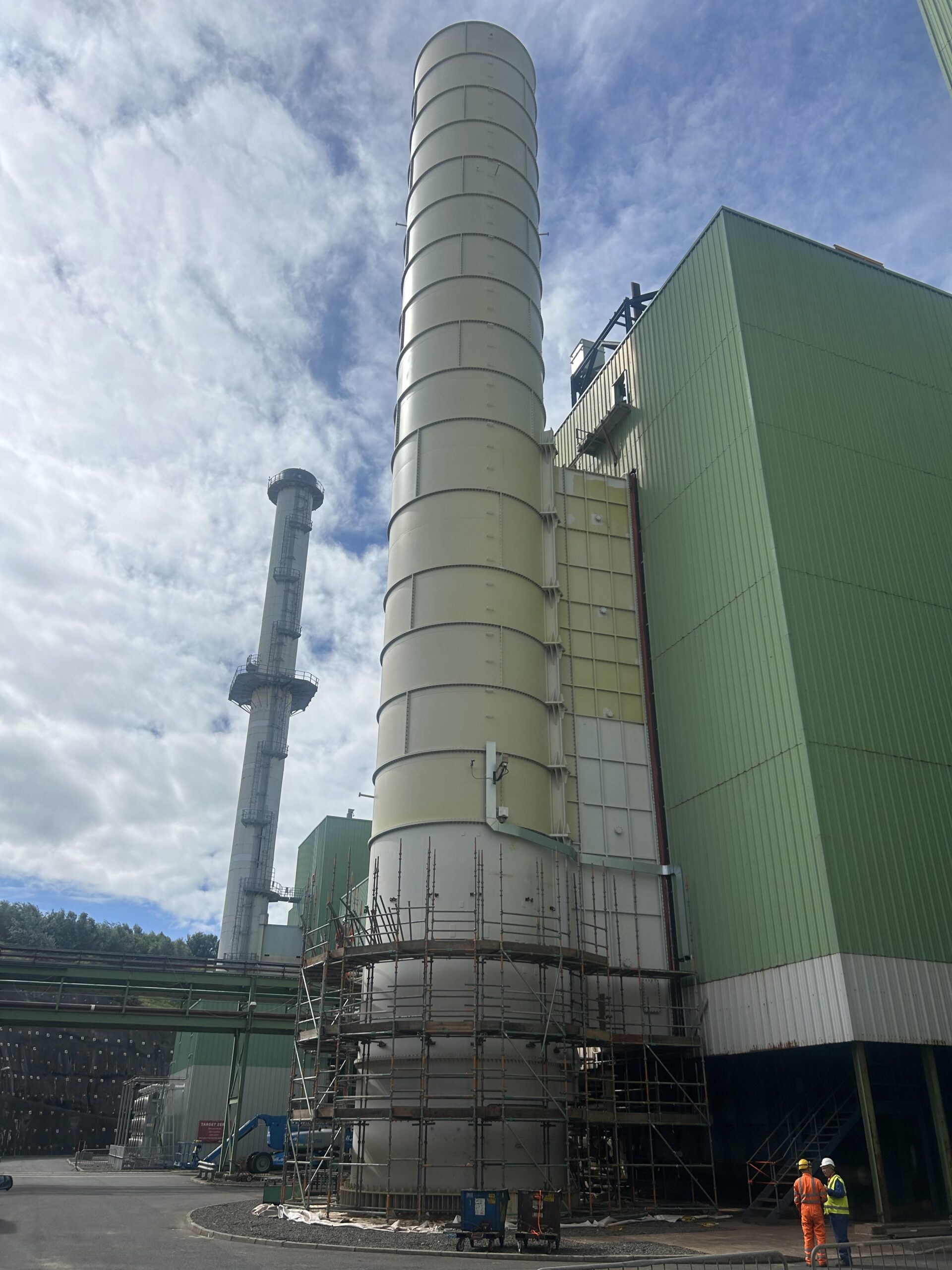